Learn about the importance of sustainable building design in “Building for the Future”. Discover how building construction and operation impact the environment and why sustainable development is crucial for future generations. Explore the symbiotic relationship between people, buildings, communities, and the natural environment for a more sustainable future.
Buildings and the Environment for Sustainable Building Design
The construction and occupation of buildings consume a significant portion of the earth’s resources and generate a considerable amount of environmental pollution. In fact, the construction and operation of buildings account for as much as one-third of the world’s energy consumption and carbon dioxide emissions, making them a significant contributor to global warming. In the United States, building operations and construction consume between one-third and one-half of the country’s energy, 70 percent of its electricity, 12 percent of its potable water, 30 percent of its raw materials, and one-third of its solid waste. These same activities are also responsible for up to 45 percent of the country’s carbon dioxide emissions. Buildings are also significant emitters of particulates and other air pollutants. In summary, building construction and operation contribute to many forms of environmental degradation and significantly burden the earth’s resources.
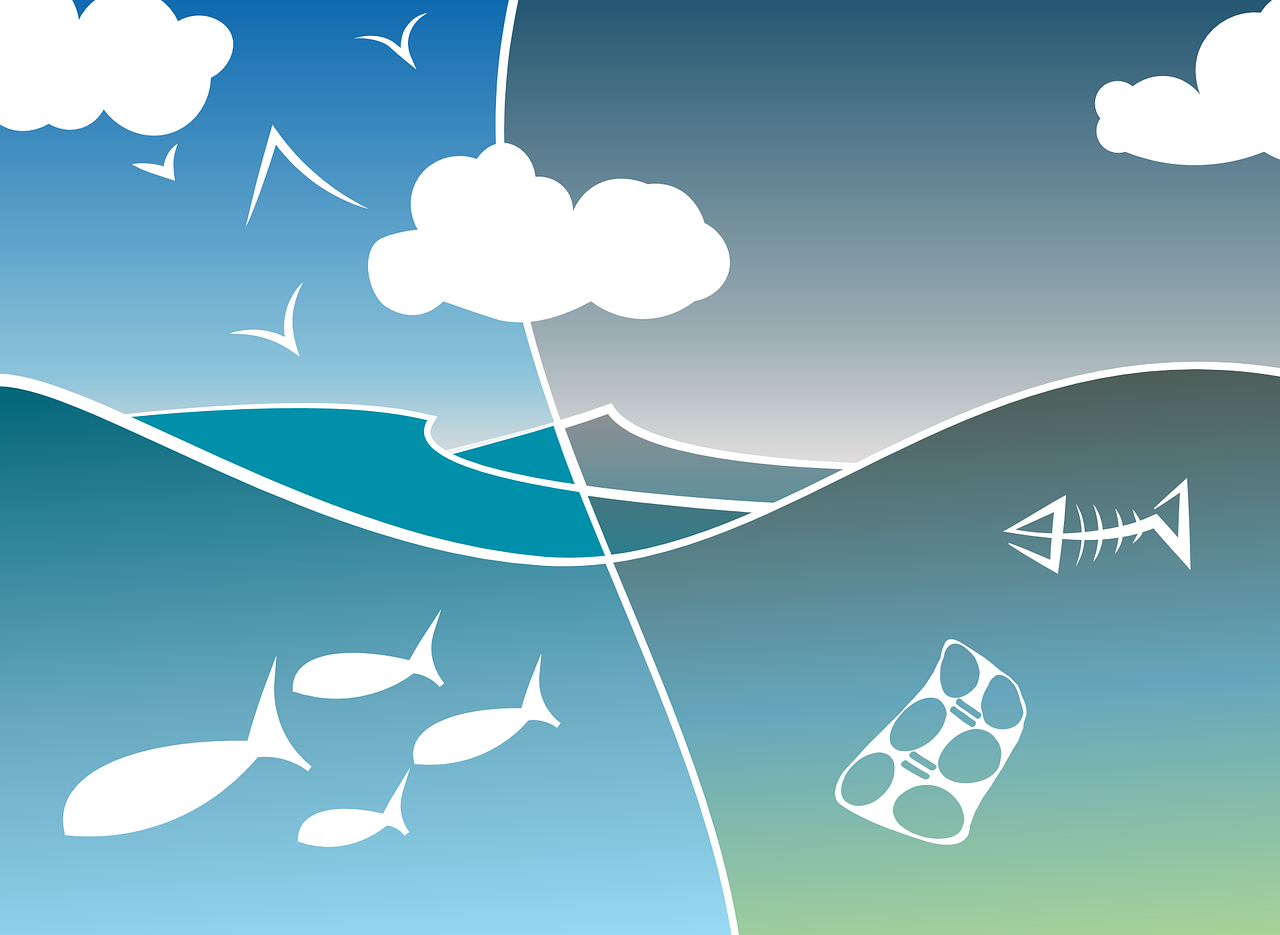
In 1987, the United Nations report “Our Common Future” provided a concise definition of sustainable development: The current building practices have been focused on meeting the needs of the present generation without considering the impact on future generations. These practices consume irreplaceable fossil fuels and other nonrenewable resources, build in sprawling patterns on prime agricultural land, use destructive land development and forestry practices that degrade natural ecosystems, generate substances that pollute water, soil, and air, and produce copious amounts of waste materials that are eventually incinerated or buried in the earth.
These practices will make it increasingly difficult for our children and their children to meet their needs for communities, buildings, and healthy lives. Sustainable building construction demands a more symbiotic relationship between people, buildings, communities, and the natural environment. Sustainable buildings—in both their construction and operation—must use less energy, consume fewer resources, cause less pollution of the air, water, and soil, reduce waste, discourage wasteful land development practices, and contribute to the protection of natural environments and ecosystems.
Over the years since “Our Common Future” was released, sustainable design and construction (also known as green building) has grown in popularity. The understanding of how buildings interact with the environment has deepened, and standards for assessing the sustainability of materials and construction practices have increased in number and matured in approach.
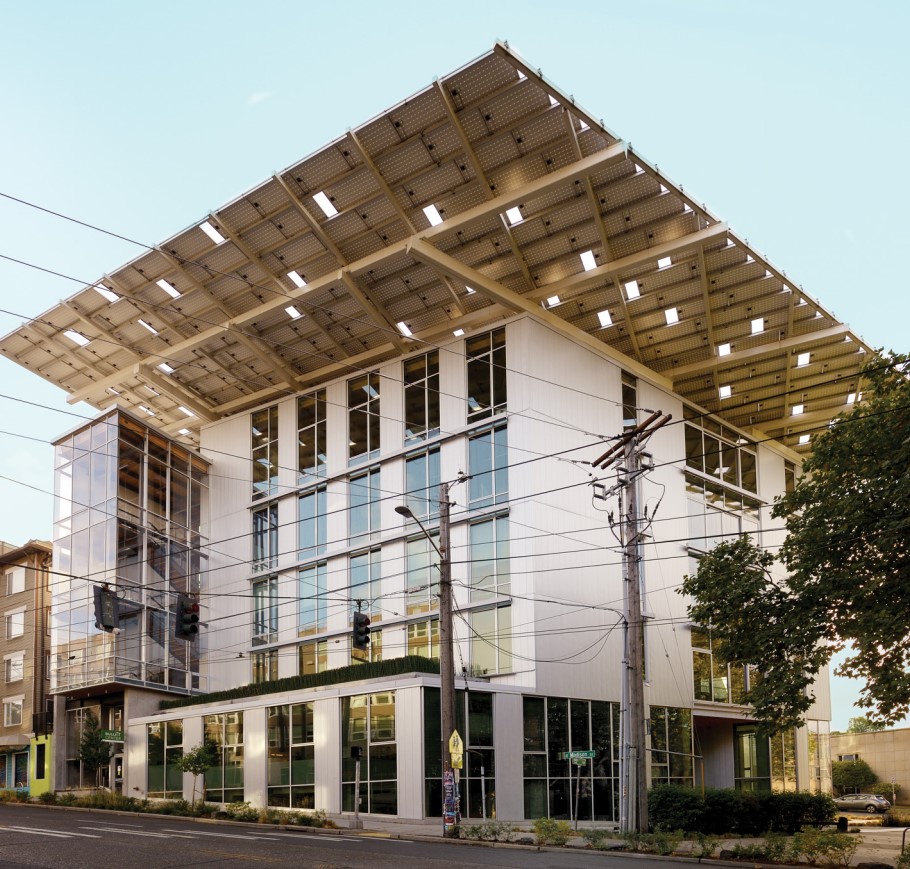
architect Miller Hull Partnership (Photo by Joe Iano.)
The definition of sustainability has expanded to include human health impacts of buildings and issues of social and economic fairness. In some cases, expectations for sustainable building performance have moved from doing less environmental harm to doing no harm or even undoing previous such harms. In other words, sustainable buildings can be designed to consume no energy or even generate excess energy, cause no air pollution or even help clean the atmosphere (Figure 1.1).
Sustainable Buildings
Over time, interest in and adoption of green buildings has broadened among public agencies, private owners, and building users. The design and construction industry has become more skilled at applying green practices, and sustainable building has become more integrated with mainstream practice. The cost and effort required to design and construct sustainable buildings continue to decrease, while their performance in terms of sustainability continues to improve.
Sustainable building requires a holistic, interdisciplinary approach to design and construction. For instance, one project goal could be to provide natural daylighting as a means of improving productivity and the well-being of building occupants. Good daylighting design reduces reliance on electric lighting, which in turn reduces electricity consumption and excess heat generated by electric lights. By implementing daylighting design techniques, it is possible to decrease cooling loads and consequently reduce the size and capacity requirements of the building’s cooling system. Moreover, daylighting design can also have an impact on the building’s overall structure and enclosure, as well as the arrangement and size of spaces within the building. Additionally, the design can also affect the placement and shape of the building itself.
As a result of the decision to provide natural daylighting, many building systems are impacted, creating many opportunities for cost savings, reductions in energy consumption, improvements in occupant health and comfort, and lessening of environmental impacts. This kind of design thinking is called integrated design process (IDP), which is a whole-systems way of working that breaks down traditional boundaries between disciplines and parts of the work. All key members of the design, construction, and owner groups are brought together to establish a clear vision and goals. The process spans from the earliest conceptual phase through design, construction, and post-occupancy (the operational phase once the project is completed). A collaborative, interdisciplinary approach is used that maximizes opportunities for synergies and innovation.
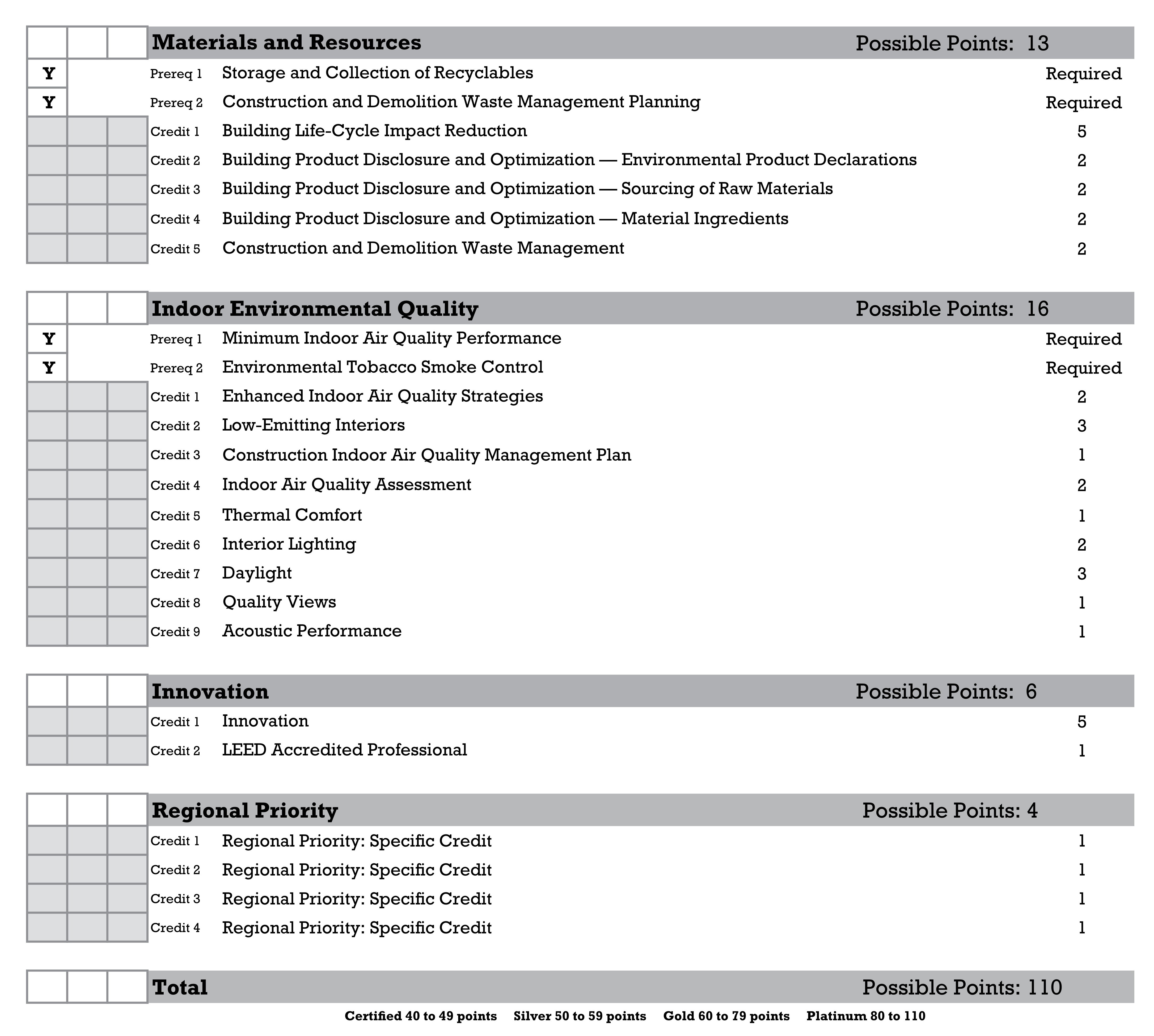
In the United States, the most widely applied program for building sustainability is the U.S. Green Building Council’s Leadership in Energy and Environmental Design (LEED) rating system. LEED for New Construction and Major Renovation groups sustainability goals into eight broad categories addressing areas such as site selection and development, energy efficiency, conservation of materials and resources, and others (Figure 1.2). Within each category are mandatory prerequisites and optional credits that contribute points toward a building’s overall rating. During the design and construction process, the achievement of prerequisites and credits is documented and submitted to the Green Building Council. The council then makes the certification of the project’s LEED compliance after construction is completed. Depending on the point total achieved, four levels of sustainable performance are recognized, including Certified, Silver, Gold, and Platinum. The LEED rating system is voluntary and is used when adopted by a private building owner or mandated by a public building agency.
The U.S. Green Building Council provides rating systems for various types of projects such as existing buildings, commercial interior buildouts, building core and shell construction, schools, retail buildings, healthcare facilities, homes, neighborhood developments, building operations and maintenance, and other project types. LEED is also implemented in Canada and other countries through affiliated organizations.

The International Living Future Institute’s Living Building Challenge™ sets a higher standard for sustainable building. This program aspires to move past making buildings that do less environmental harm to those that do no harm or even improve the natural environment and our well-being. For example, a building constructed and operated to this standard will (when considered on an annualized basis) generate all its own energy from on-site renewable resources, consume no fresh water, and have no greenhouse gas emissions.
The Living Building Challenge is a framework that consists of seven categories, known as Petals. These Petals include Place, Water, Energy, Health & Happiness, Materials, Equity, and Beauty, each of which is broken down into 20 Imperatives. These Imperatives cover a wide range of sustainability aspects, such as net zero energy, responsible sourcing of materials, and embodied carbon footprint. The certification process offers three levels of recognition, starting with Living Building Certification, which meets all Imperatives relevant to the building type. Petal Certification, on the other hand, represents a lower level of compliance, while Zero Energy Certification applies to projects that produce all their energy on-site, without relying on combustion processes. To obtain certification, a building must be operational for at least one year, during which its real-world performance is evaluated. Additionally, the Living Building Challenge can be applied to various types of construction and development, including neighborhoods, landscapes, infrastructure projects, and building renovations.
Sustainable Building Materials
To design sustainable buildings, it is necessary to consider the environmental and health impacts of the materials used in their construction. When choosing a material, designers should ask questions such as: Does the material’s manufacturing rely on non-renewable resources, or can it be made from recycled or rapidly renewable materials? Will the transportation of this material require additional energy from a distant location, or can it be sourced locally? Are there any toxic ingredients present in the material that may produce harmful emissions, or is it free of any health concerns?
Information about building materials and products can come from different sources and take various forms:
- It may be self-reported by the product manufacturer, or it may come from an independent, trusted third party.
- It may take the form of a neutrally expressed, transparent disclosure of material attributes, or it may gauge the merits (or demerits) of such attributes and provide a rating of the material’s sustainability.
- It may address a limited scope of concerns, or it may describe the full range of impacts of material throughout its life cycle from raw materials extraction to end-of-life disposal or repurposing.

The industry-standard Product Data Sheet (PDS) is a simple example of manufacturer self-reported information. The PDS provides a description of a product, its material makeup and physical properties, and guidelines for use. It may also include information relevant to sustainability concerns, although this is not its main purpose. The scope of information provided in a PDS is left entirely to the manufacturer, and the information is not independently verified.
The Material Life Cycle and Embodied Impacts
Preparing environmental product and building declarations depends on accounting for the environmental impacts of materials and products throughout their life cycles. This process begins with raw materials extraction, continues with manufacture, construction, and use, and finishes at the end of life when a material is disposed of or put to a new use. One of the most comprehensive methods for quantifying the environmental impacts associated with materials and buildings is life-cycle analysis (LCA), or cradle-to-grave analysis. Through each life-cycle stage, impacts are tallied: How much fossil fuel, water, electricity, and other materials are consumed? How much global warming gases, solid waste, and other air and water pollutants are generated? The total of all these impacts describes the environmental footprint of the material (Figure 1.3).
The concept of embodied energy also comes from life-cycle analysis. Embodied energy is the total amount of energy consumed during a material’s life cycle. Since energy consumption often correlates with the consumption of nonrenewable resources and the generation of greenhouse gases, it’s easy to assume that materials with lower embodied energy are better for the environment than those with greater embodied energy. However, when making such comparisons, it’s important to ensure that the comparison is functionally equivalent. For example, a material with an embodied energy of 10,000 BTU per pound isn’t necessarily environmentally preferable to another with an embodied energy of 15,000 BTU per pound if two pounds of the former material are required to accomplish the same purpose as one pound of the latter.
When considering the environmental impact of materials, it’s important to take into account the types of energy consumed for each material, such as fossil, nuclear, or renewable energy. Embodied energy and other life-cycle effects may sometimes be calculated for only a part of the material life cycle. A cradle-to-gate analysis begins with materials extraction but extends only as far as when the material leaves the factory, excluding the effects of transportation to the building site, installation, maintenance, use, and disposal or recycling.

Although less comprehensive, such analyses can still provide a useful basis for comparison between products. For many materials, the difference in embodied energy between a cradle-to-grave and cradle-to-gate analysis is small since most of the energy expenditure occurs prior to the material’s installation, use, and eventual disposal.
The concept of embodied effects can also be applied to other measured inputs or outputs from a life-cycle analysis. For instance, embodied water refers to the amount of fresh water consumed as a result of building with a particular material. While life-cycle analysis is the most comprehensive materials assessment method available today, it doesn’t necessarily address all impacts that arise from using a material or product. For example, LCA of wood products doesn’t capture the loss of biodiversity, decreased water quality, or soil erosion caused by poor forestry practices.
In such cases, sustainable forestry certification programs are better suited to address these concerns. Additionally, while global warming potential is quantified in a material environmental product declaration, the ultimate consequences of that effect for ecosystems, wildlife populations, and human well-being aren’t fully described.
Health Impacts of Building Materials

Information related to the human health impacts of materials and products can be conveyed in various formats, much like the sources of information used for evaluating the environmental effects of materials. Manufacturers or independent agencies can create health product declarations (HPDs) in a manner similar to environmental product declarations. The HPD Collaborative, an independent organization with input from multiple construction industry stakeholders, defines the standard for creating HPDs. HPDs furnish reliable and consistent information about the composition of materials and the associated risks to human health and the environment. They itemize the contents of the product and highlight associated hazards, such as the presence of carcinogens, persistent bio-accumulative toxic compounds, respiratory irritants, neurotoxins, and other harmful substances. HPDs, like EPDs, do not function as certification or rating tools that determine the healthfulness of a product on their own. However, they do offer crucial information in a standardized format that is useful for making health-related comparisons.
The Impact of Sustainable Buildings
Sustainable building practices have demonstrated significant positive outcomes in building performance. Post-occupancy evaluations conducted on US buildings constructed according to LEED standards indicate energy consumption and greenhouse gas emission reductions in the range of 25-35% as compared to national averages. Other noteworthy enhancements have been observed in areas such as decreased water usage, reduced operating costs, heightened occupant satisfaction, increased property values, and more. However, sustainable building also presents novel challenges. Newly formulated materials may be less durable than their predecessors, and sourcing innovative products from alternative suppliers may be costly and difficult. Additionally, limited familiarity with green building technologies can lead to errors in design or construction. It is equally critical to ensure that sustainable buildings fulfill their performance expectations. While the average performance of sustainable buildings surpasses that of conventional structures, individual building performance often varies significantly from these benchmarks. Although many green buildings outperform traditional ones, several do not meet the anticipated outcomes.
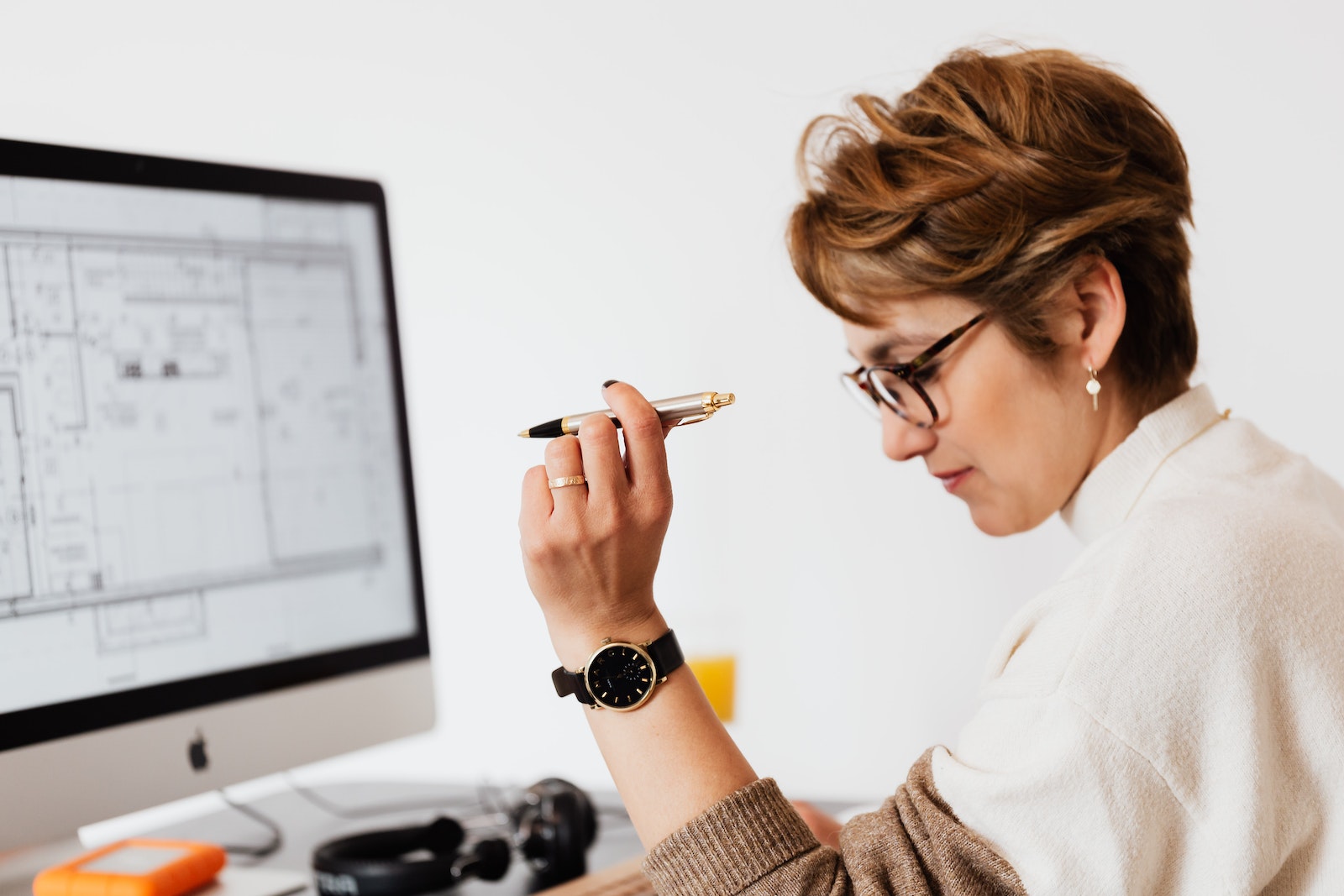
Building commissioning, abbreviated as Cx, is a crucial process that ensures the fulfillment of performance expectations in completed buildings. The commissioning process starts with the definition of performance objectives at the beginning of the design phase. These objectives are then employed to guide decision-making and review progress at interim milestones during the design process. Towards the end of the construction process, on-site testing is carried out to verify actual performance. Finally, operational guidance is provided to ensure that the finished, occupied building functions as intended.
Traditionally, building commissioning has been associated with testing and verifying heating, ventilating, and air conditioning (HVAC) systems in newly constructed buildings. However, with sustainable design, the focus is on achieving integrated, whole-building performance, addressing a broader range of building systems and objectives. An effective, fully documented commissioning process is a prerequisite for achieving LEED certification. Under the Living Building Challenge, a full year of operational data, showing successful compliance with design and performance objectives, must be collected before awarding Living Building certification.
The Work of the Design Professional
The process of constructing a building begins with an idea in someone’s mind – a desire for new and spacious accommodations for a family, organization, or enterprise. For larger buildings, the owner typically engages the services of building design professionals. An architect helps to organize the owner’s ideas about the new building while various engineering specialists work out concepts and details of foundations, structural support, and mechanical, electrical, and communications services.
Environmental and Land Use Regulations
An environmental impact assessment might be the initial step in the legal approval process for many buildings. Various issues pertaining to the built environment and the natural environment may be discussed, such as potential effects on water resources, protected species, natural habitats, air and water pollution, municipal water and sewer systems, transportation systems, urban open space, community facilities, and more. Impact analyses highlight potentially undesirable consequences, provide opportunities for stakeholder input, and offer a legal framework for putting forward mitigating measures. Depending on the size of the project and the difficulty of the issues at hand, the scope of the issues addressed and the amount of work necessary to complete an impact assessment can vary greatly.

In many places, buildings must also abide by zoning ordinances, which are rules governing how land is used. These regulate the types of activities that are permitted on a specific parcel of land, the amount of the land that may be covered by buildings, the distance that buildings must be set back from property lines, the number of parking spaces that must be provided, the size of the total floor area that may be constructed, and the height of the buildings. In larger cities, zoning ordinances may include special conditions such as fire zones with additional fire safety regulations, neighborhood enterprise districts with financial incentives for new construction or the renovation of existing structures, or other special circumstances.
Building Codes
Local governments also control construction through the use of building codes. Building codes establish minimum requirements for construction quality, structural integrity, durability, livability, and, in particular, fire safety in order to protect the public’s health and safety.
The majority of building codes in North America are based on one of many model codes, which are standardized codes that local jurisdictions can use instead of creating their own. The Canadian Commission on Building and Fire Codes publishes the National Building Code of Canada in Canada. The majority of the provincial and municipal building codes in that nation are based on it.
The International Building Code® (IBC) is the most widely used model code in the United States. Local code officials from all over the nation are members of the International Code Council, a private, nonprofit organization that publishes this code. It serves as the foundation for the majority of state, local, and municipal building codes in the United States. The information in this book about building codes is based on the IBC.
The IBC begins by outlining the following building occupancies:
- A-1 through A-5 Assembly: public performance spaces like theaters, auditoriums, lecture halls, nightclubs, restaurants, places of worship, libraries, museums, sports stadiums, and so forth.
- B Business: establishments like banks, executive offices, college and university buildings, post offices, and professional offices.
- E Educational: schools for grades K through 12 as well as some daycare facilities for kids.
- F-1 and F-2 Factory Industrial: processes use materials with a moderate degree of flammability and noncombustibility, respectively.
- H-1 through H-5 High Hazard: Occupancies that pose a high risk include those that contain explosive, toxic, or highly flammable materials.
- I-1 through I-4 Institutional: settings include 24-hour residential care facilities, hospitals, nursing homes, prisons, and some daycare centers where residents may need assistance in the event of a building emergency.
- M Mercantile: shops, markets, service stations, salesrooms, and other retail and wholesale establishments.
- R-1 through R-4 Residential: structures include apartment complexes, dorms, hotels, one- and two-family homes, and assisted-living facilities.
- S-1 and S-2 Storages: facilities for the storages of moderate- and low-hazard materials, respectively.
- U Utility and Miscellaneous: agricultural structures, carports, greenhouses, sheds, stables, fences, tanks, towers, and other auxiliary structures.
Different levels of life-safety hazard in buildings are identified by the IBC when describing occupancies. For instance, a hospital must be built to a higher standard of safety than a hotel or motel occupied by people with physical abilities since patients there are bedridden and unable to escape a fire on their own. A warehouse that houses noncombustible materials and is occupied by few people who are all accustomed to their surroundings must be built to a higher standard than a large retail mall building that contains large quantities of combustible materials and is occupied by many users of varying ages and physical capacities. A primary school needs more security for its occupants than a university. In comparison to a university building, an elementary school needs more protection for its occupants. Emergency exits need to be considered more carefully in a theater than they would in a typical office building due to the close quarters and dark surroundings.
A list of construction type definitions follows these occupancy classifications. Type I construction, which is made with materials that are highly fire resistant and noncombustible, is at the top of this list. The least fire-resistant of all construction types, Type V is built at its base from combustible light wood framing. Types II, III, and Type IV fall between these two extremes in terms of fire resistance.
After defining occupancies and construction types, the IBC goes on to specify which occupancies can be housed in which types of construction, as well as under what restrictions regarding building height and area. For many different combinations of occupancy and construction type, the starting values for the maximum building height and area per floor are summarized in Figure 1.4. The maximum permitted size for a building of any specific use and type of construction can be determined once the values in this table have been modified in accordance with other code provisions.
Think about an office building, for instance. This building is designated as Occupancy B, Business, according to the IBC. We can tell right away by reading across the table from left to right that Type I-A construction can be used to build this building to any desired height and area without restriction.
The IBC defines Type I-A construction as being made entirely of noncombustible structural materials, such as masonry, concrete, or steel, and as having the necessary fire resistance. However, wood is not allowed to be used in this type of construction (with a few exceptions) because it is combustible. A listing of the necessary fire resistance ratings, measured in hours, for various parts of our proposed office building can be found under Type I-A construction in the upper table of Figure 1.5, which was reproduced from the IBC. The first table row, for instance, specifies that the structural frame, which includes components like columns, beams, and trusses, must be rated for 3 hours.
A 3-hour resistance is also required for bearing walls in the second row, which support the floors or roofs above. The third row indicates that Table 602, which specifies fire resistance rating requirements based on proximity to neighboring buildings or properties, must also be followed by exterior walls. (The lower half of Figure 1.5 contains Table 602). The other rows of the table define the minimum specifications for the construction of floors and roofs, as well as interior nonbearing walls and partitions that do not support any loads from above.
By using noncombustible structural materials and having the highest fire resistance ratings, Type I-A construction is the least flammable, as shown in Tables 601 and 602 in Figure 1.5. We can see other construction types by reading across the table; some have lower fire resistance ratings and others have fewer restrictions on the use of combustible materials. We find Type V-B construction at the very right of the table, where any structural material—both combustible and noncombustible—is allowed, and no fire protection is necessary. Figure 1.4 illustrates these differences, with Type I-A construction being allowed to reach the highest height and largest area while other construction types that are more vulnerable are restricted to progressively smaller heights and areas.
The design of these parts can move forward using building assemblies that meet the fire resistance rating requirements once the requirements for the major components of a building have been established. A number of sources, including the IBC, as well as catalogs and handbooks published by building material manufacturers, construction trade associations, and organizations concerned with fire protection of buildings, are used to calculate the fire resistance ratings for building materials and assemblies. To ensure consistency of results, each rating is the result of extensive laboratory tests that were conducted in accordance with a recognized standard protocol. (ASTM E119 is the most significant of these tests.
Examples of how these ratings are frequently presented are shown in Figure 1.6.
Generally speaking, the higher the level of fire resistance needed for a building, the more expensive it will be. Buildings are typically designed to have the lowest level of resistance allowed by the building code. Type I-A construction could be used to create our imagined office building, but is this level of quality really required?
Assume the owner wants a three-story structure with 30,000 square feet on each floor. Looking at Figure 1.4’s table, we can see that in addition to Type I-A construction, the building can also be Type I-B construction, which allows for a building with 11 stories and an unlimited amount of floor space, or Type II-A construction, which allows for a building with 5 stories and 37,500 square feet per floor. However, Type II-B construction is prohibited and only permits structures with three stories and 23,000 square feet per floor. It can also be constructed using Type IV-HT, but not Type III or Type V.
These decisions are affected by additional variables. In many cases, the tabulated area per floor for a multistory building or quadrupled for a single-story building, if a building is completely protected by a fully automatic sprinkler system for the suppression of fire. The additional safety to life and property provided by such a system serves as the justification for this permitted increase.
In most cases, if such a sprinkler system is installed, the height limit is also increased by one story. If such a sprinkler system is provided for the three-story, 30,000 square foot office building that we have been considering, some simple math will show that all construction types shown in Figure 1.4 except Type V can be used to build it.
A further increase of up to 75% in allowable area is granted in accordance with another formula if more than 25% of the building’s perimeter walls face public ways or open spaces that can be reached by fire-fighting equipment. Additionally, each divided portion of a building may be treated as a separate building for the purposes of computing its allowable area if it is divided by fire walls having the fire resistance ratings specified in another table (Figure 1.7). This effectively allows the construction of a building that is many times larger than what Figure 1.4 would initially suggest. (For simplicity’s sake, additional factors in figuring out the IBC’s allowable building height and area have been left out of these examples.)
The IBC also sets standards for structural design, the building of floors, walls, and ceilings, chimney construction, the installation of fire-protection systems, accessibility for people with disabilities, and many other significant facets of building design. The International Residential Code for One- and Two-Family Dwellings (IRC), a streamlined model code addressing the construction of detached one- and two-family homes and townhouses of limited size, is another publication of the International Code Council in addition to the IBC. These codes may be directly adopted in their model form by any specific building agency. Alternately, they may be adopted with amendments, maintaining the code’s overall structure and intent while adapting it to the needs of that jurisdiction.
A new building must adhere to additional codes in addition to the building code. Building energy efficiency standards are established by energy codes, which have an impact on a designer’s decisions regarding windows, heating and cooling systems, and numerous other aspects of the construction of a building’s enclosing walls and roofs. One of the key factors in enhancing building sustainability is the creation of stricter energy codes that mandate buildings use less energy due to the significant environmental effects associated with building energy consumption.
Health codes govern the design and operation of sanitation-related features in public buildings like swimming pools, dining establishments, schools, or healthcare facilities. Building operations and maintenance are governed by fire codes to guarantee that egress routes, fire-protection systems, emergency power, and other life-safety systems are kept in good working order.
The design and installation of building electrical, plumbing, heating, and cooling systems are governed by electrical and mechanical codes. Similar to the earlier discussed building codes, some of these regulations may be written locally, but the majority are based on international standards. In fact, figuring out which authorities have authority over the project and what codes and regulations are applicable is a crucial step in the early design of any significant building.
FAQ
What is sustainable building design?

Sustainable building design involves creating buildings that minimize their impact on the environment while maximizing their efficiency, functionality, and durability. This includes using environmentally-friendly materials, reducing energy consumption, and incorporating features that support human health and well-being.
Why is sustainable building design important?

Sustainable building design is important because it helps to reduce the environmental impact of buildings, which account for a significant amount of energy consumption and carbon dioxide emissions worldwide. It also supports the health and wellbeing of occupants and helps to conserve natural resources.
How does sustainable building design help the environment?
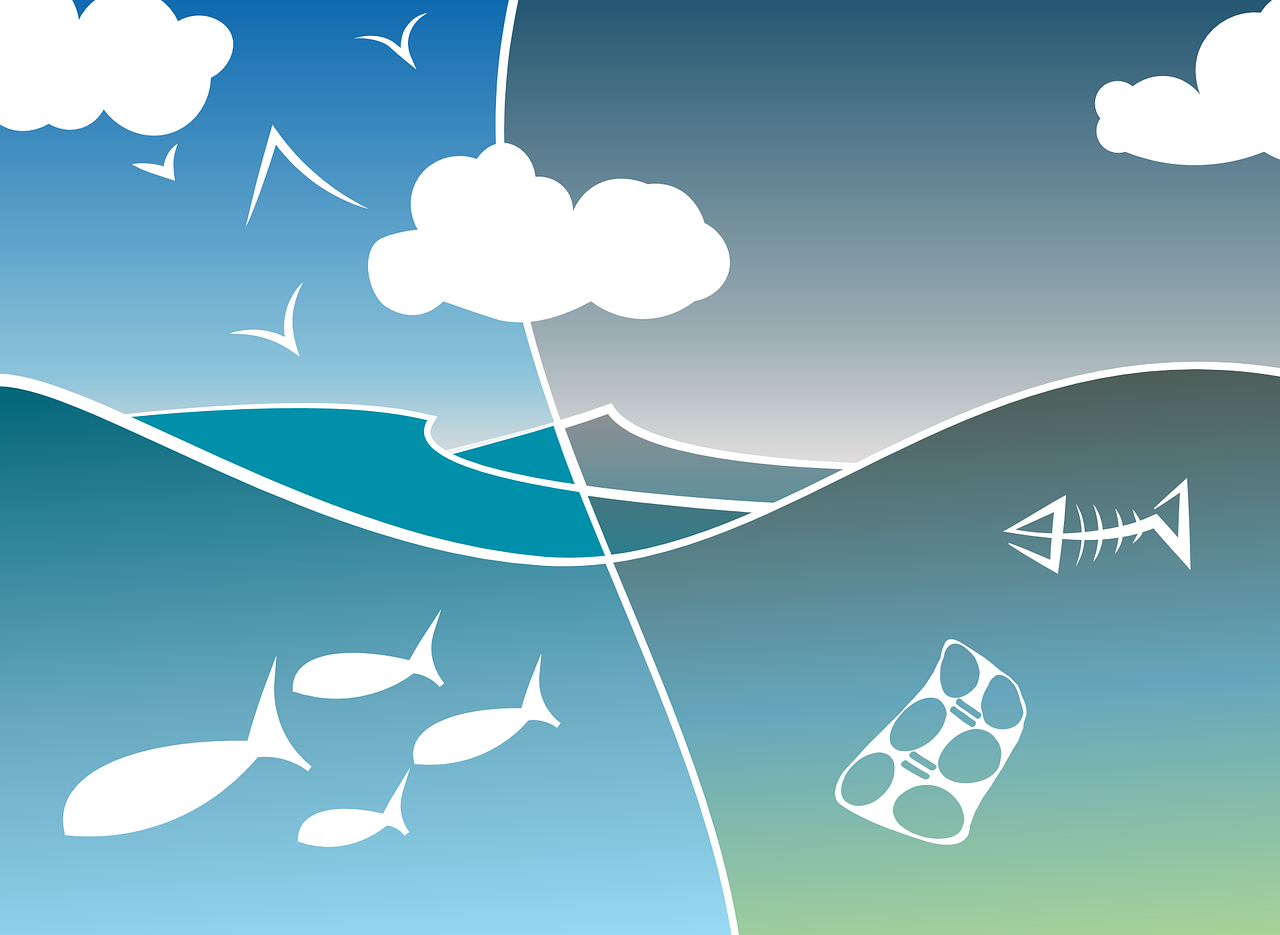
Sustainable building design helps the environment by reducing the amount of energy needed to operate buildings, which reduces greenhouse gas emissions and air pollution. It also conserves natural resources by using environmentally-friendly materials, reducing waste, and protecting natural ecosystems.
What are some features of sustainable building design?
Features of sustainable building design may include energy-efficient heating and cooling systems, solar panels, green roofs, rainwater harvesting systems, low-flow plumbing fixtures, and the use of sustainable building materials like bamboo, recycled steel, and salvaged wood.
How can I incorporate sustainable building design into my own building projects?
There are many ways to incorporate sustainable building design into your own projects, including using environmentally-friendly materials, maximizing natural lighting, incorporating energy-efficient systems, and designing for adaptability and long-term durability. Working with a knowledgeable architect or contractor can also help ensure that your project is designed and built with sustainability in mind.